İçerikte Neler Var?
YODA: Yalın Olgunluk Değerlendirme Analizi
Günümüz iş dünyası, rekabetin giderek arttığı bir ortamda faaliyet göstermektedir. Şirketler, daha fazla verimlilik elde etmek, maliyetleri azaltmak ve müşteri memnuniyetini artırmak için sürekli olarak yeni yöntemler arayışındadır. Bu noktada, Yalın Üretim Metotları önemli bir rol oynamaktadır.
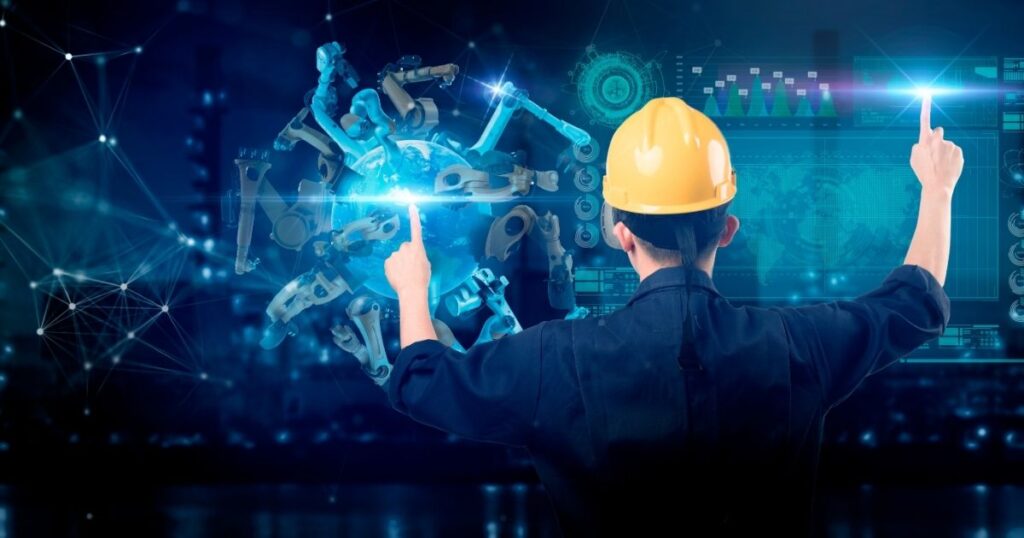
Yalın, Japon otomotiv endüstrisinde geliştirilen bir üretim felsefesi olarak başlamış, ancak daha sonra pek çok sektörde başarılı bir şekilde uygulanmıştır. Yalın Dönüşüm, bir işletmenin tüm süreçlerini ve operasyonlarını daha verimli hale getirmek amacıyla Yalın Üretim Metotlarını benimsemesi ve uygulaması anlamına gelir. Temel hedef, atıl kaynakları azaltmak, iş süreçlerini optimize etmek ve müşteri taleplerine daha hızlı ve daha iyi yanıt vermek olarak özetlenebilir. Yalın Dönüşüm, işletmelerin maliyetleri azaltmasına, kaliteyi artırmasına ve rekabet avantajı elde etmesine yardımcı olur.
Üretimde verimliliğin arttırılması ve dijital dönüşüm sürecinin hızlandırılması Türkiye’nin en önemli kalkınma gündemlerinden biridir. Bu alanda geliştirilen politikalara katkı sağlamak amacıyla T.C. Sanayi ve Teknoloji Bakanlığı, Stratejik Araştırmalar ve Verimlilik Genel Müdürlüğü, Birleşmiş Milletler Kalkınma Programı (UNDP), Ticaret ve Sanayi Odaları işbirliği ile yürütülen “Uygulamalı KOBİ Yetkinlik Merkezi-Model Fabrika Projesi” kapsamında çalışmalar yürütülmektedir. Bu çalışmalara ek olarak KOSGEB İşletme Geliştirme destek programı kapsamında firmaların Yalın olgunluk seviyelerini artırmaya yönelik hibe desteği başlatılmıştır.
Destek kapsamında;
1-Firmanın Yalın olgunluk seviyesinin tespit edilmesine yönelik Yalın Olgunluk Değerlendirme Analiz Raporu (YODAR) hazırlanması. (Rapor başına 10.000 TL’ye kadar %100 oranında destek)
2-YODA sonucu 50 ve altında puan alan işletmelere Yalın Sistemler konusunda belirlenen başlıklar altında Model Fabrikalar üzerinden eğitim verilmesi (70.000 TL’ye kadar %80 oranında destek)
3-YODA sonucu 50 üzerinde puan alan işletmelere Model Fabrikaların Öğren-Dönüş programı kapsamında danışmanlık hizmeti sağlanması (150.000 TL’ye kadar %80 oranında destek) sağlanmaktadır.
Model Fabrika gerçek bir üretim ortamında deneyimsel öğrenme teknikleri kullanılarak operasyonel mükemmeliyet ilkelerinin öğretilmesini ve yaygınlaştırılmasını sağlayan bir eğitim ve danışmanlık merkezidir. Sürekli iyileştirme yaklaşımı ile verdiği eğitim ve danışmanlık hizmetleri sayesinde, işletmelerin insan, makine, hammadde, malzeme, zaman ve enerji kaynaklarını en verimli şekilde kullanmalarını ve rekabet güçlerini artırmalarını amaçlamaktadır.
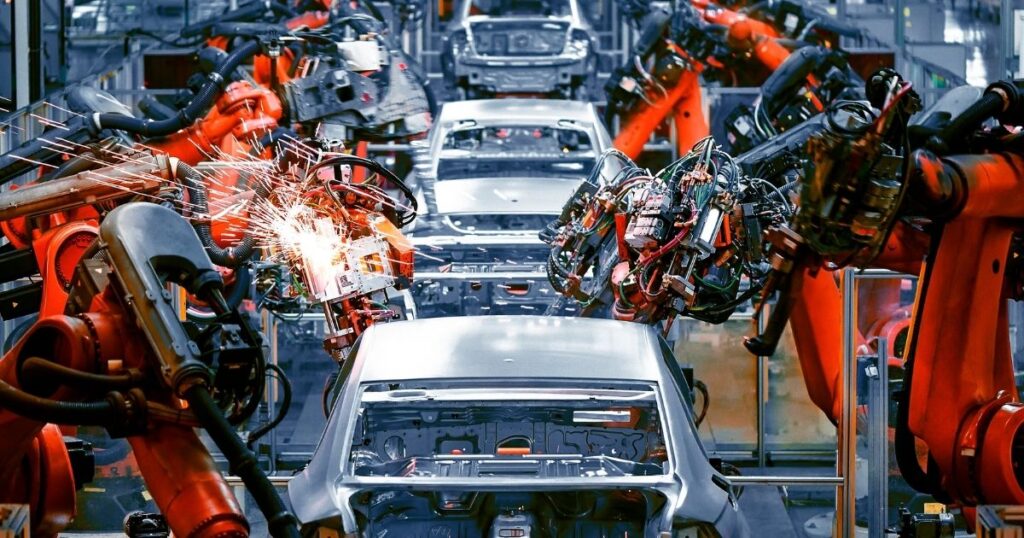
Yalın üretimin ana felsefesi, işletmelerde üretim ve hizmet sürecini israflardan arındırarak maliyetlerin düşürülmesi, müşteri memnuniyetinin arttırılması ve sürekli iyileştirmenin sağlanmasıdır. Yalın Üretim, Toyota’da geliştirilen ve daha sonra diğer işletmelerde uygulanan bir üretim felsefesidir. Yalın Üretim Metotları; Değer akış haritalama, OEE, TPM, SMED, Gemba, Kaizen, Jidoka, 5S, Yamazumi ve Heijunka gibi temel prensiplere dayanır.
Değer Akış Haritalama (Value Stream Mapping-VSM); Değer Akış Haritalama, özellikle üretim süreçlerini iyileştirmek için kullanılan süreç analizi aracıdır. Değer Akış Haritalama, iş süreçlerini ayrıntılı bir şekilde görselleştirmek, anlamak ve geliştirmek için kullanılır. Hammaddeden müşteriye üretim akışı ve ürün geliştirme süreci, her bir ürün için geçerli olan temel akışlar olarak tanımlanmaktadır. Değer akışı haritalandırma, bir değer akışındaki değeri, israfı ve israf kaynaklarını görmek ve tek bir prosesten daha fazlasını göz önünde canlandırmak için başvurulan bir yöntemdir. Değer akışı bakış açısı, yalnızca parçalar üzerinde değil büyük resim üzerinde çalışmayı ve bütünü iyileştirmeyi gerektirir.
TPM (Toplam Verimli Bakım); Kuruluşa, iş değeri katan makineler, ekipman, süreçler ve çalışanlar aracılığıyla üretim, güvenlik ve kalite sistemlerinin bütünlüğünü koruma ve geliştirme sistemidir. Üretim süreçlerindeki beklenmedik arızaları ve gecikmeleri önlemek için tüm ekipmanları en iyi çalışma durumunda tutmaya odaklanır.
OEE (Genel Ekipman Etkinliği); Üretim işleminin, çalışmasının planlandığı dönemlerde tam potansiyeline kıyasla ne kadar iyi kullanıldığının bir ölçüsüdür. Gerçekten verimli olan üretim süresinin yüzdesini belirlemektedir. Arızalar, ekipman ayarları, duruşlar, çalışma hızındaki azalmalar, ıskartalar ve yeniden işlem gibi kayıplar üzerine düşerek, makine ve ekipmanların performanslarının arttırılması hedeflenmektedir.
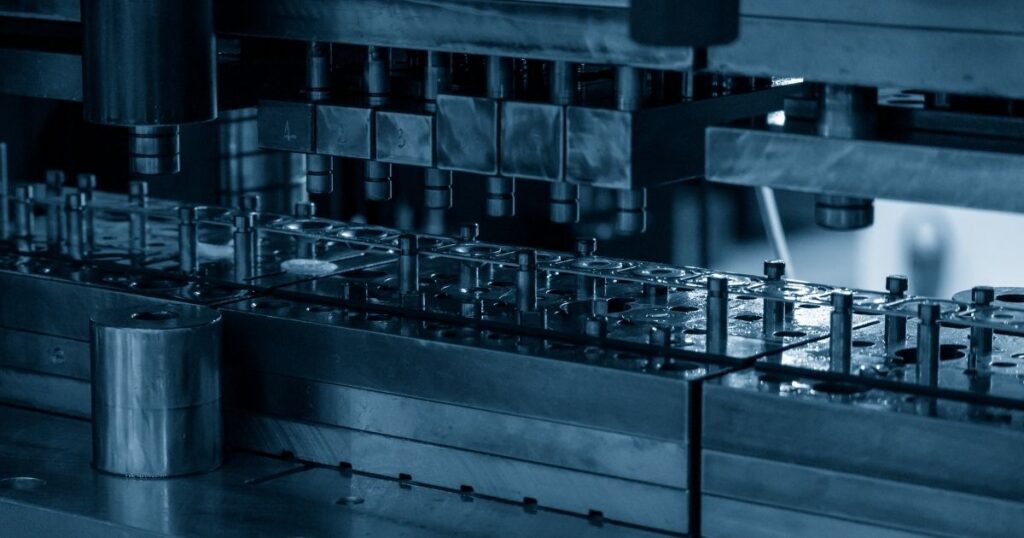
SMED (Single-Minute Exchange of Die); Makinenin durmasına sebebiyet veren her türlü periyodik değişim işlemini kısaltmak amacıyla uygulanabilecek bir tekniktir. SMED, özellikle üretim hatlarında ürünlerin hızla değiştirilmesi gereken durumlarda, kaynakların (zaman, işgücü, malzeme) israfını azaltmayı ve süreç verimliliğini artırmayı amaçlar. Setup (kurulum), bir evvelki partiden çıkan son parça ile yeni partiden çıkacak ilk kalite onaylı parçayı elde etmek için gerekli işlemleri yapma, ekipmanları değiştirme sürecidir.
SMED ile, iş emirleri arası tip değişimleri ve setup süreleri kısalmakta, daha düşük lot büyüklükleri ile üretim yapılması sağlanmakta, düşük lot büyüklükleri ile müşteri sipariş değişkenliklerine esneklik artırılmakta, teçhizatın üretim kapasitesi artırılmakta, yarı mamul ve mamul stok miktarı azaltılmaktadır. Üretimde esneklik ve çeviklik sağlayan SMED ile model değişimine harcanan zaman kısaltılarak üretim verimliliği artırılmaktadır.
Gemba; Japonca Gemba kelimesi, değerin yaratıldığı yeri ifade etmektedir. Sorunların görünür olmasını ve en iyi iyileştirme fikirlerinin gembaya giden yollardan çıkacağı düşüncesiyle üretimde gemba yürüyüşleri gerçekleştirilmektedir. Gemba yürüyüşleri gerçek süreci görme, işi anlama, soru sorma ve öğrenme eylemini ifade etmektedir.
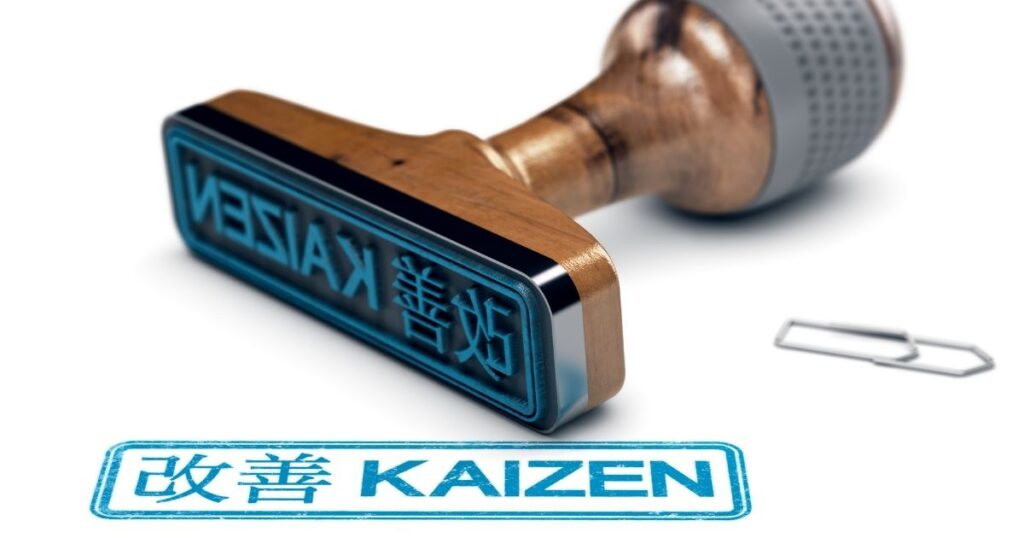
Kaizen (Sürekli İyileştirme); Kaizen, belirli bir zaman diliminde müşteri memnuniyetinin arttırılması ve rekabet güçlerinin etkilenmesi amacıyla süreçlere yönelik, çalışan, süreç, zaman ve teknolojide gelişme sağlamayı ve maliyetlerde düşmeyi ifade eden bir kavramdır. Japonca bir birleşik sözcük olan kaizeni oluşturan sözcüklerden kai değişim, zen ise daha iyi anlamına gelmektedir. Kaizen, özellikle üretim endüstrisi olmak üzere birçok sektörde başarıyla uygulanmış bir felsefedir. Çalışanların katılımı ve liderlik desteği ile sürekli iyileştirme süreci, atıkları azaltmak, maliyetleri düşürmek, kaliteyi artırmak ve rekabetçi olmayı sağlamak için kullanılır. Ayrıca, kaizenin temel prensipleri ve yöntemleri, hizmet sektörü ve diğer organizasyonlarda da etkili bir şekilde uygulanabilir.
Jidoka (Otonomasyon); Üretim hattını durdurma yetkisinin işçiye veya makineye verilmesidir. Otonomasyon kavramı zaman zaman otomasyon kavramı ile karıştırılmaktadır. Otonomasyon, makineye insan zekası ve duyarlılığını kazandırmaktır. Jidoka, üretim esnasında herhangi bir anormallik halinde, tasarlanan sistemin devreye girerek makineyi durdurması yada sesli veya ışıklı uyarı vermesidir. Tasarlanan bu araçlara Poka-Yoke sistemi denmektedir. Böylece kontrolörün ve tasarlanan operasyonun istemeden yapacağı ve hatalara sebep olacağı durumları, bu mekanizmalarla %100 önleyip ortadan kaldırmaktadır. Amaç bir sorun tespit edildiğinde daha fazla israfa neden olmadan hattın durdurulmasıdır.
5S; Organizasyonlarda kaliteli bir çalışma ortamı oluşturmak ve sürekliliğini sağlamak için geliştirilen bir tekniktir. Çalışma koşullarını performans, konfor, güvenlik ve temizlik açılarından en iyi duruma getirmeyi amaçlar. Ayrıca temiz ve organize bir çalışma ortamı sağlayarak israfın ve değişkenliğin azalmasını sağlar. Çalışma alanlarının temiz, düzenli ve amaca uygun biçime sokulması için uygulanan bir verimlilik metodolojisi olan 5S, Japonca Seiri, Seiton, Seiso, Seiketsu, Shitsuke kelimelerinden oluşur.
Yamazumi (Hat dengeleme); Yamazumi, iş adımlarının zaman ölçüm değerleri kullanılarak takt zamanına ve diğer kısıtlara uygun şekilde dengelenmesidir. İş dengelemesi sonucunda üretim hızı ayarlanırken kişi başı düşen iş yükü dengelenir. Yamazumi; İşlerin ögelerine ayrılması, Takt zamanının hesaplanması, İş dengeleme grafiğinin oluşturulması, Mevcut durumun iyileştirilmesi adımlarından oluşur.
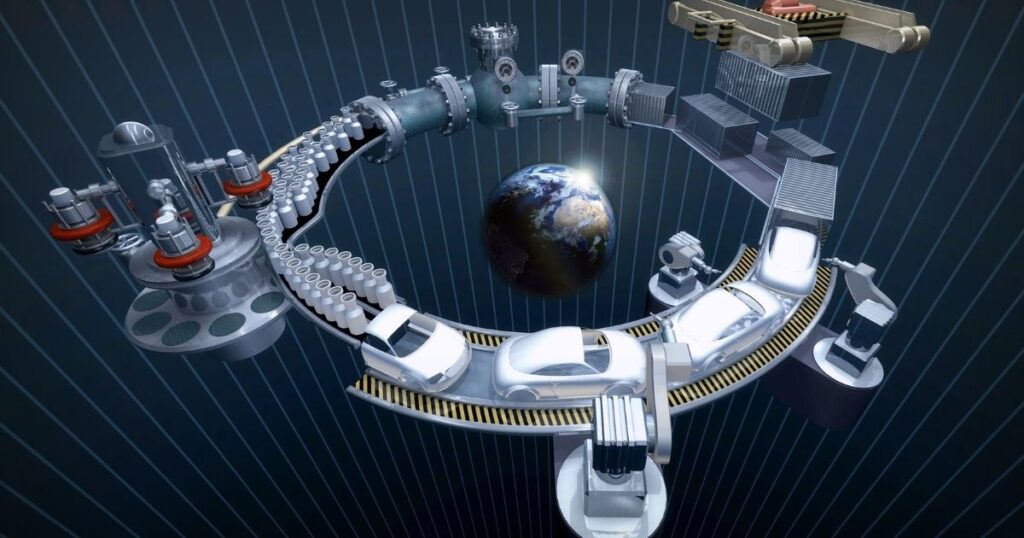
Milk Run (Malzeme besleme); Milk Run, taşıma işlemi gerçekleştirilecek olan ürünleri tek bir araçta birleştirerek verimlilik elde etmeyi amaçlayan bir lojistik tedarik yönteminin genel adıdır. Milk Run, ismini sokak aralarında belirli bir rota ile evlere süt dağıtan ve tekrar süt kaplarını belirli bir rota ile toplayan süt araçlarından almaktadır.
Heijunka (Karışık Yükleme); Heijunka, yalın üretimde siparişler doğrultusunda üretimin seviyelendirilmesi anlamına gelmektedir. Heijunka üretimi düzgünleştirerek üretimdeki kaynakları daha etkin kullanarak değer zincirini verimli hale getirmeyi amaçlar. Talep değişikliklerine hazırlıklı olmak ve bunu stok birikmelerine yol açmadan üretimle senkronize edebilmek, yalın üretim işletmelerinde Heijunka tekniği kullanılarak mümkün olmaktadır.
Heijunka’nın Faydaları; Talebin istenen zamanda yapılabilme esnekliği sağlanır. Talepler dengelenir, öngörülebilirlik artar. Müşteri talebi kadar üretim yapıldığı için stok ve depolama maliyeti azalır. Satılmayan ürün riski azalır. Makine ve işgücü dengeli kullanılır, israflar azalır. Malzeme ihtiyaç planlama, kapasite planlama ve çizelgeleme süreçleri çalıştırılarak, hem kaynaklar en etkin şekilde kullanılır, hem de hedeflenen müşteri siparişleri zamanında karşılanarak, müşteri memnuniyeti sağlanır.
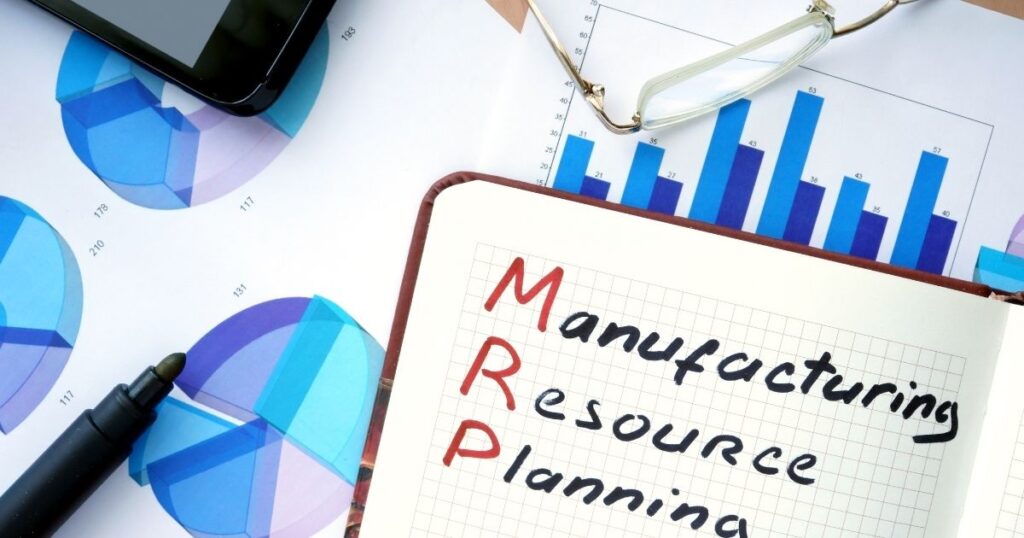
MRP (Malzeme İhtiyaç Planlaması); Bilgisayar destekli bir bilgi sistemi olup bitmiş ürün isteklerini zamana bağlı alt montaj, parça, hammadde vb. isteklerine dönüştürmektedir. Bu yöntem müşterilere ürünlerin teslim süresinden geriye doğru çalışmaktadır. Buna bağlı olarak tedarik süresi ve diğer bilgiler yardımıyla ne zaman ve ne kadar sipariş verilmesi gerektiğini belirlemeye çalışmaktadır.
CRP (Kapasite Gereksinim Planlaması); Ana üretim programında ve malzeme ihtiyaç planında somutlaşan üretim hedeflerine ulaşmak için gerekli personel ve üretim aracı kapasitesini belirleme sürecidir.
MRP, Kanban ve CRP kullanılmasıyla kaynakların etkin kullanılması sağlanır. Stok miktarlarında azalma olur. Dar boğazlarda azalma olur. İnsan ve sermaye kaynakları daha etkin kullanılır. İşletmenin her şeye sahip olması yerine sadece ihtiyacı olan ürünlere sahip olmasını sağlar. Nakit ihtiyacı planlamasında etkinlik artar.
Süreç yaklaşımı, organizasyonların işleyişini ve yönetimini anlamak ve iyileştirmek için kullanılan bir yönetim yaklaşımıdır. Bu yaklaşım, organizasyonları iş süreçleri merkezli bir perspektifle ele alır ve iş süreçlerinin etkin bir şekilde tasarlanması, yönetilmesi ve sürekli olarak iyileştirilmesi gerektiğini vurgular. Süreç yaklaşımı, kalite yönetimi, iş mükemmelliği ve sürekli iyileştirme felsefelerinin temelini oluşturur. Standardizasyon ile iş öğelerinin tanımlanması, standart operasyon prosedürlerinin oluşturulması ve uygulama sistematiği oluşturulur. Standart iş yapış şekilleri, yöntemler ile standart çıktı elde edilmesini ve yetkinliklerin artırılmasını sağlamaktadır.
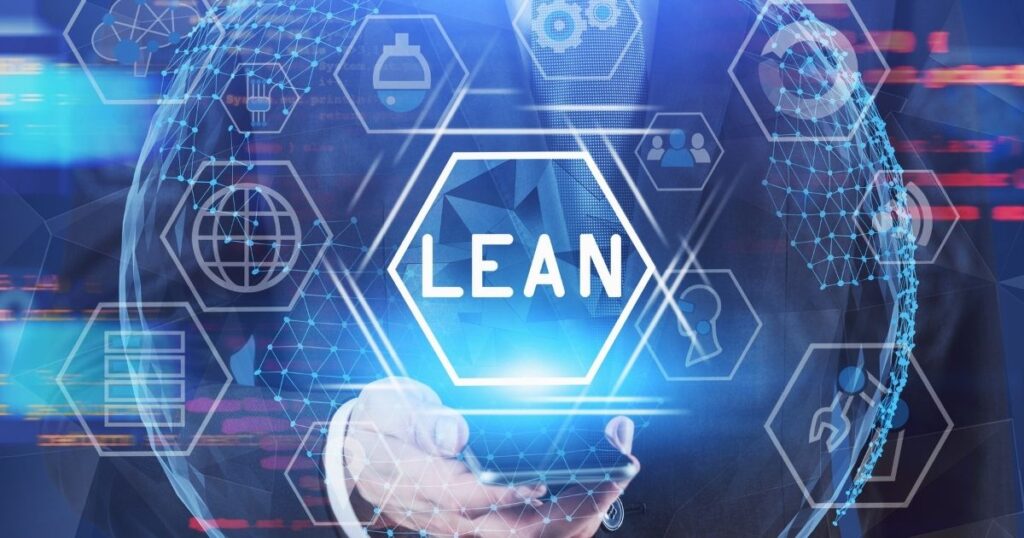
Sonuç olarak yalın dönüşüm, işletmeler için önemli bir rekabet avantajı sağlama özelliği kazandırır. Yalın Üretim Metotları, maliyetleri azaltmak, hızı artırmak, kaliteyi yükseltmek ve müşteri memnuniyetini artırmak için etkili bir yol sunar. İşletmeler, bu metotları benimseyerek verimliliği artırabilir ve başarıya giden yolda önemli bir adım atabilir.
Dr. Nuri Şişman
Lisans öğrenimini Eskişehir Osmangazi Üniversitesinde Çiftanadal programıyla 2002 yılında Makine Mühendisliği ve 2001 yılında Kimya Mühendisliğinde tamamladı. Makine Enerji Anabilim dalında 2005 yılında yüksek lisans ve 2018 yılında doktorayı tamamladı. 2010 yılında Uludağ Üniversitesinde İşletme yüksek lisansını tamamladı.
20 yılı aşkın profesyonel kariyerinde; Proje Yönetimi, Ar-Ge Merkezi kurulma ve sürdürme çalışmaları, TÜBİTAK, Ar-Ge ve süreç geliştirme projelerini koordinesi ve yönetimi, projelerin teknik ve mali fizibilite analizlerini oluşturulması çalışmalarını sürdürdü. Yeni ürün geliştirmenin koordine edilmesi, deneysel tasarım ve gelişmiş istatistiksel araçları kullanarak sonuçların analiz edilmesi, risk yönetimi araçlarını kullanarak tasarım ve süreç çalışmalarını yürütülmesi, kalite yönetim sistemini kurulması ve yönetilmesi faaliyetlerinde bulundu.
6 sigma karakuşak sahibi olarak birçok sürekli iyileştirme projelerini yönetti. TÜBİTAK TÜSSİDE tarafından organize edilen eğitim ve sınavlar sonucu Yalın Dönüşüm Danışmanı olarak çalışma hakkı kazandı. Bunun yanı sıra İş Güvenliği-A ve Enerji Yöneticisi sertifikaları bulunmaktadır. İş hayatında üretim, kalite, mühendislik, iş geliştirme departmanlarında görev aldıktan sonra 2016 yılından beri Otomotiv yan sanayinde Ar-Ge Merkezi Koordinatörü olarak çalışmaktadır.
Kamu üniversitelerinde akreditasyon ve dış danışman kurul üyesi olarak deneyimlerimi aktarmaktadır. Altı adet tescillenmiş patenti ve yapmış olduğu projelerle ilgili enerji, tasarım ve üretim alanlarında makaleleri bulunmaktadır.
[…] genellikle iş dünyası, üretim, kalite yönetimi ve sürekli gelişim bağlamında kullanılır. Kaizen, sürekli olarak küçük adımlarla iş süreçlerini ve iş yapış şekillerini iyileştirme […]